Making Leather Sheaths - Part 3
Two sheaths of three are finally finished, thus today I will shortly write about dyeing and finishing them.
Firstly I sanded all outlines to 100 grit and I knocked off all edges. After that, I applied alcohol-based dyes.
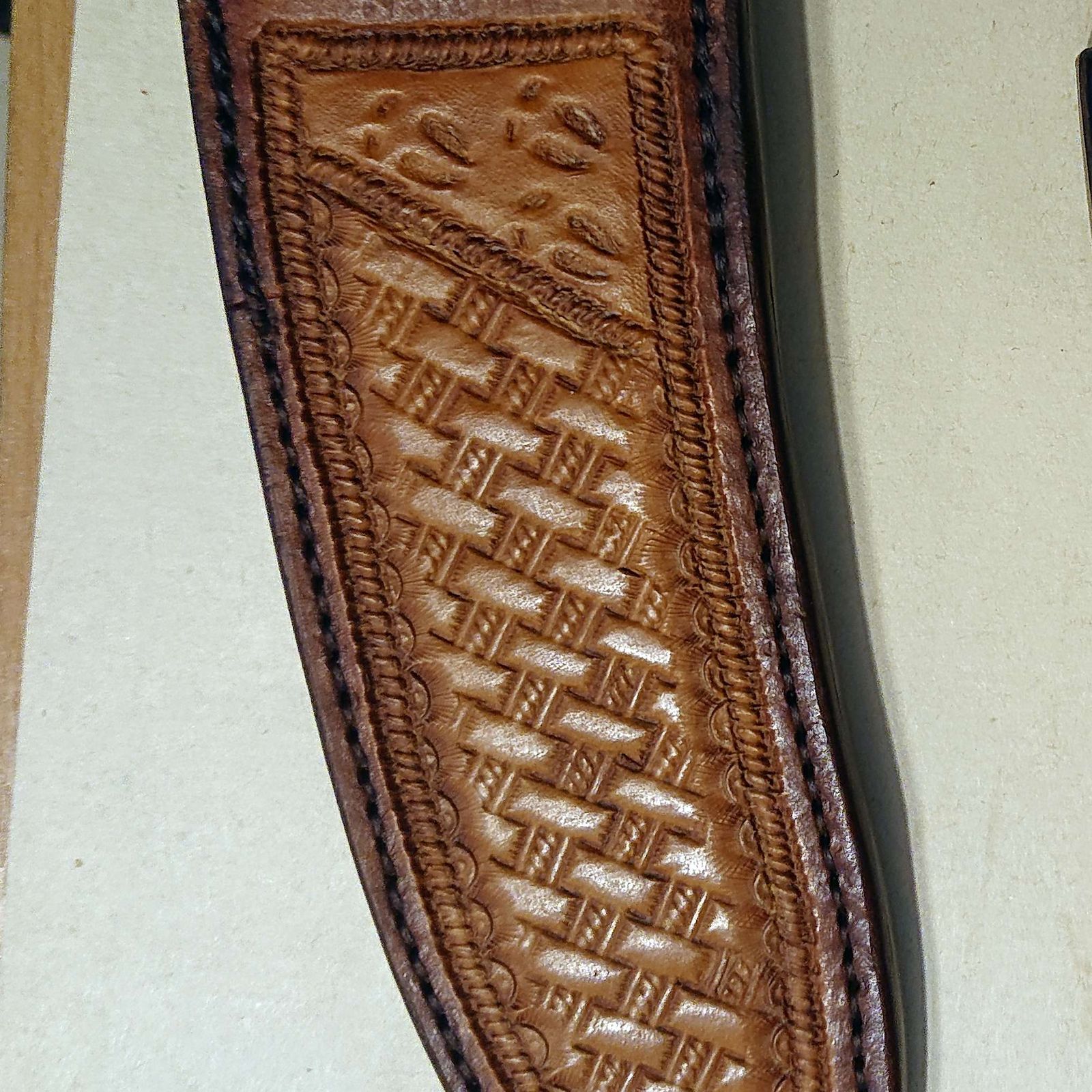
These two sheaths have
similar patterns and color schemes – light oak brown basket weave
pattern and mahogany brown outlines. To dye them thoroughly, I
applied several coats, which took some time.
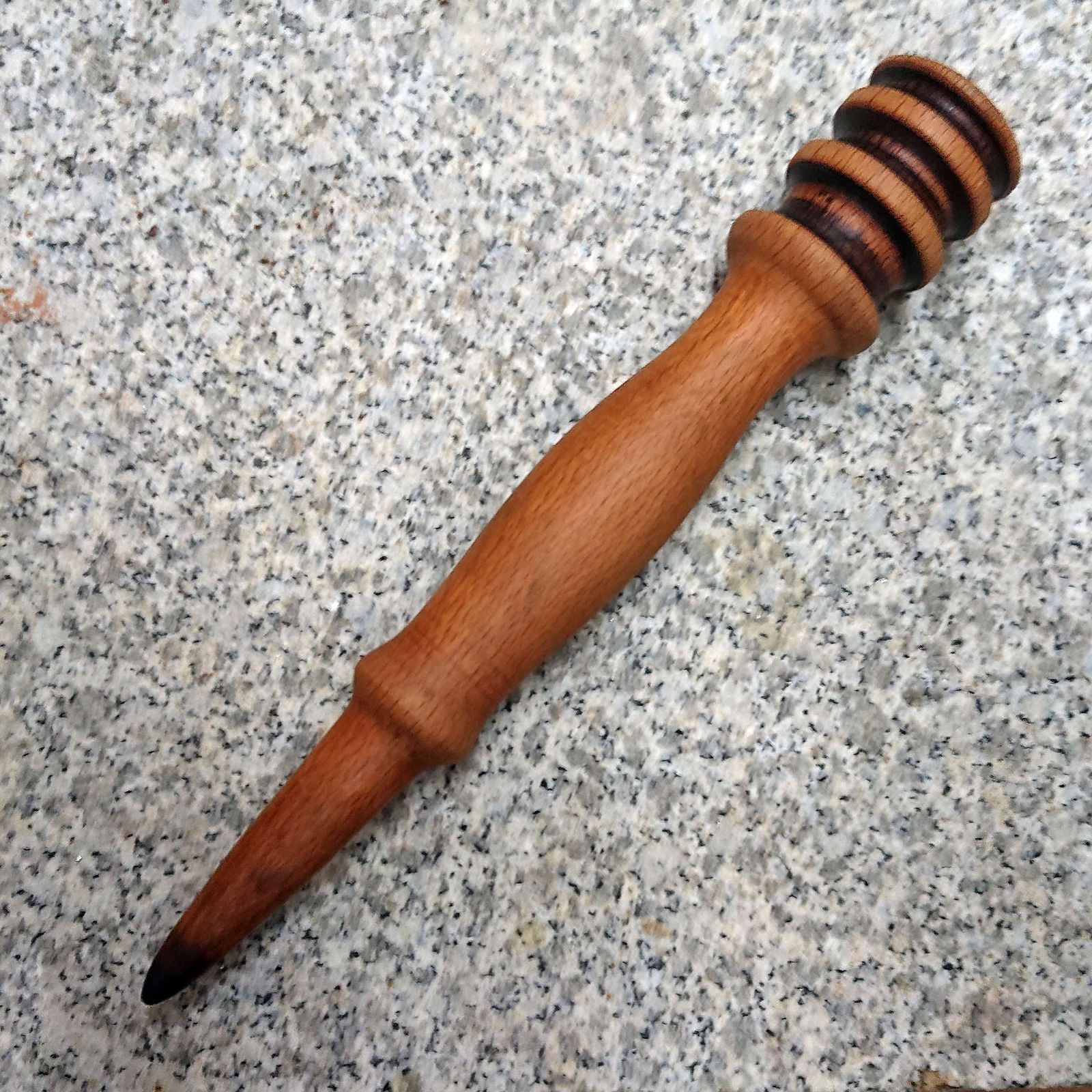
Once the sheaths were
dyed, I could polish the edges with a wooden burnisher. For the best
result, it is good to wet the edges first, but not too much, just the
amount it takes for the burnishing itself to dry them again. It is
possible to speed up this process by using a burnishing wheel on a
drill, but I did not get around to making one yet, thus I am doing it
the old way.
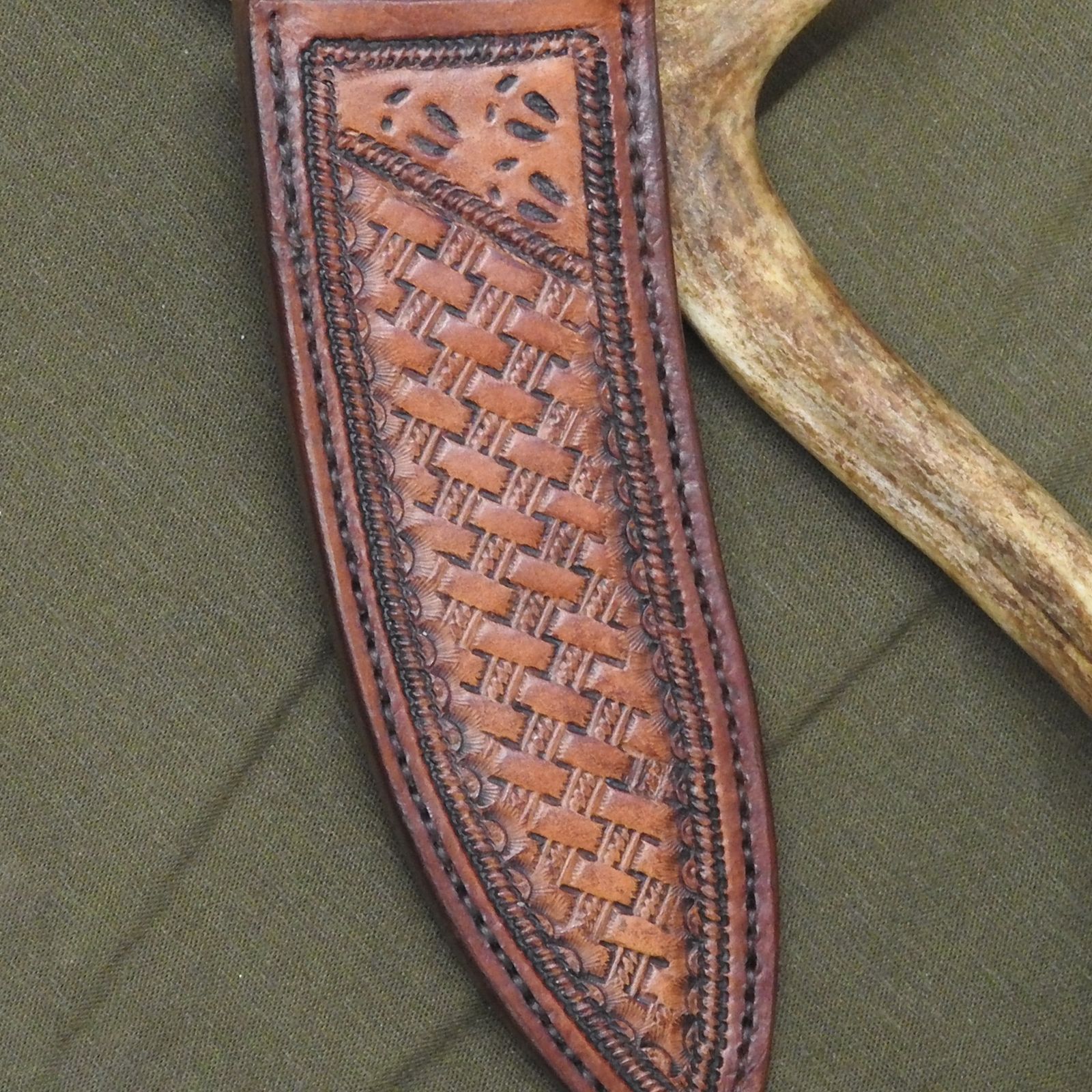
Once all edges are
burnished, it is possible to apply a surface coat for waterproofing. I
am using dubbin made from pig fat, olive oil, and beeswax. After 2-3
coats it is possible to polish the leather but for these, I applied
some additional dye – gel patina. Patina is a dye with a thick
consistency that after application can be scraped off with some
straight surface (like a dowel wrapped in a paper towel) so it only
stays in indentations. That accentuates the stamped decorations,
especially the basket weave.
Once the patina dried out, I applied a few dubbin layers again and that was it.
I haven't decided yet about next week's topic. Maybe about the third sheath that is currently in production, maybe something else.