Making a Commission - Part 5 - Polishing
Polishing is a knife-maker's bane.
Blade polishing is the main reason why hand-made knives are so expensive and take so long to make. If the blade is to be worth a damn, it needs to have a good-looking surface finish. And achieving that on hardened and tempered steel is not exactly a walk in the park.
The first problem is that the blades inevitably get deformed in the quench. That is the main reason why I am quenching blades under 3 mm thick between plates – this reduces the deformations to a minimum. However some deformations occur even so because the blades are not perfectly symmetrical, they do not have perfectly uniform temperature and the quenching foil does not allow for a perfect contact with the quenching medium.
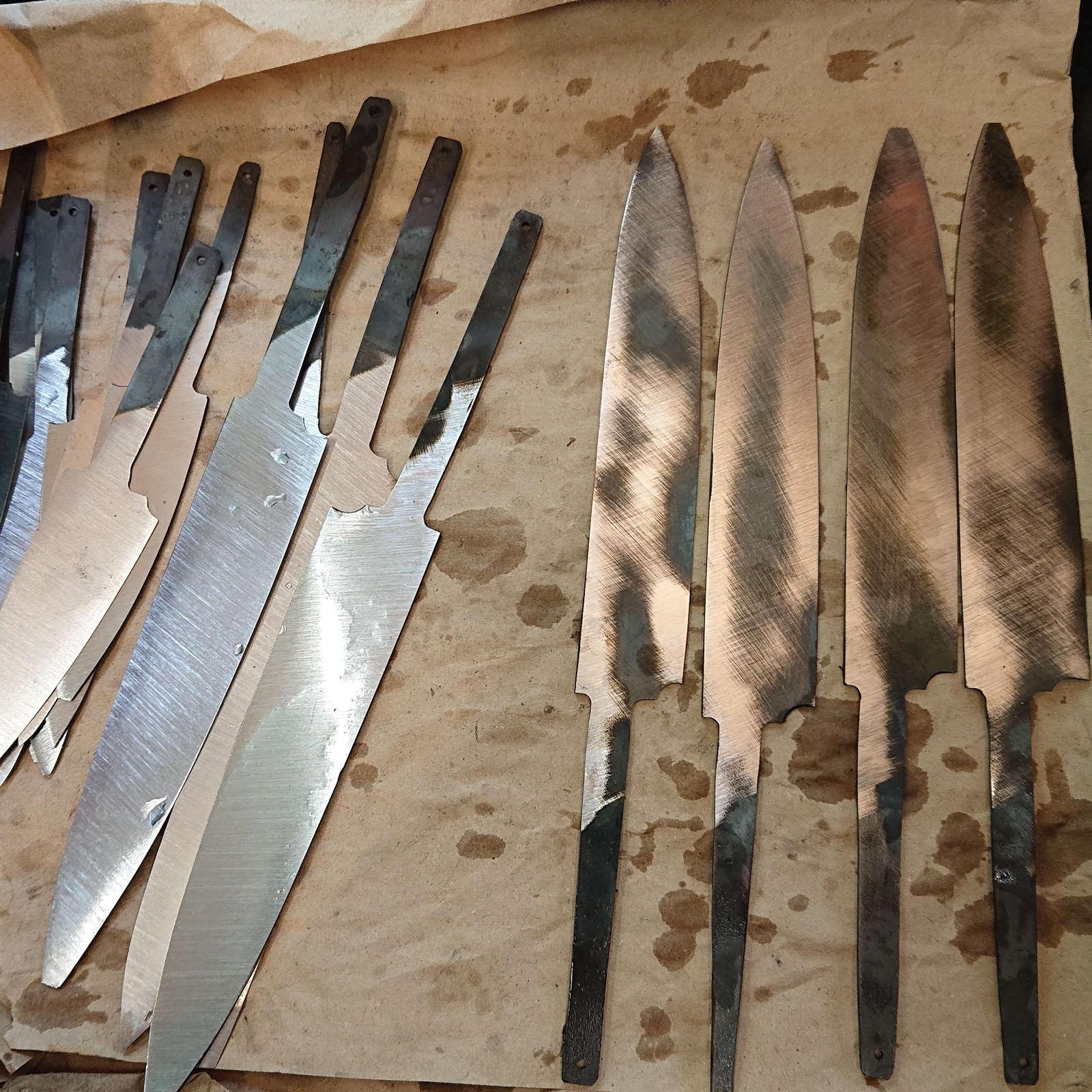
In the picture on the right this can be seen – I run these blades only once/twice over an abrasive belt so the high points were ground down but the low points sill are darkened with oxidation from tempering. Quenching these thin blades in oil would exacerbate these deformations and they could very well be irreparable and I would have to discard some of the blades. Plate quenching keeps them within a few tenths of an mm so they can be ground out without making the blades unusably thin.
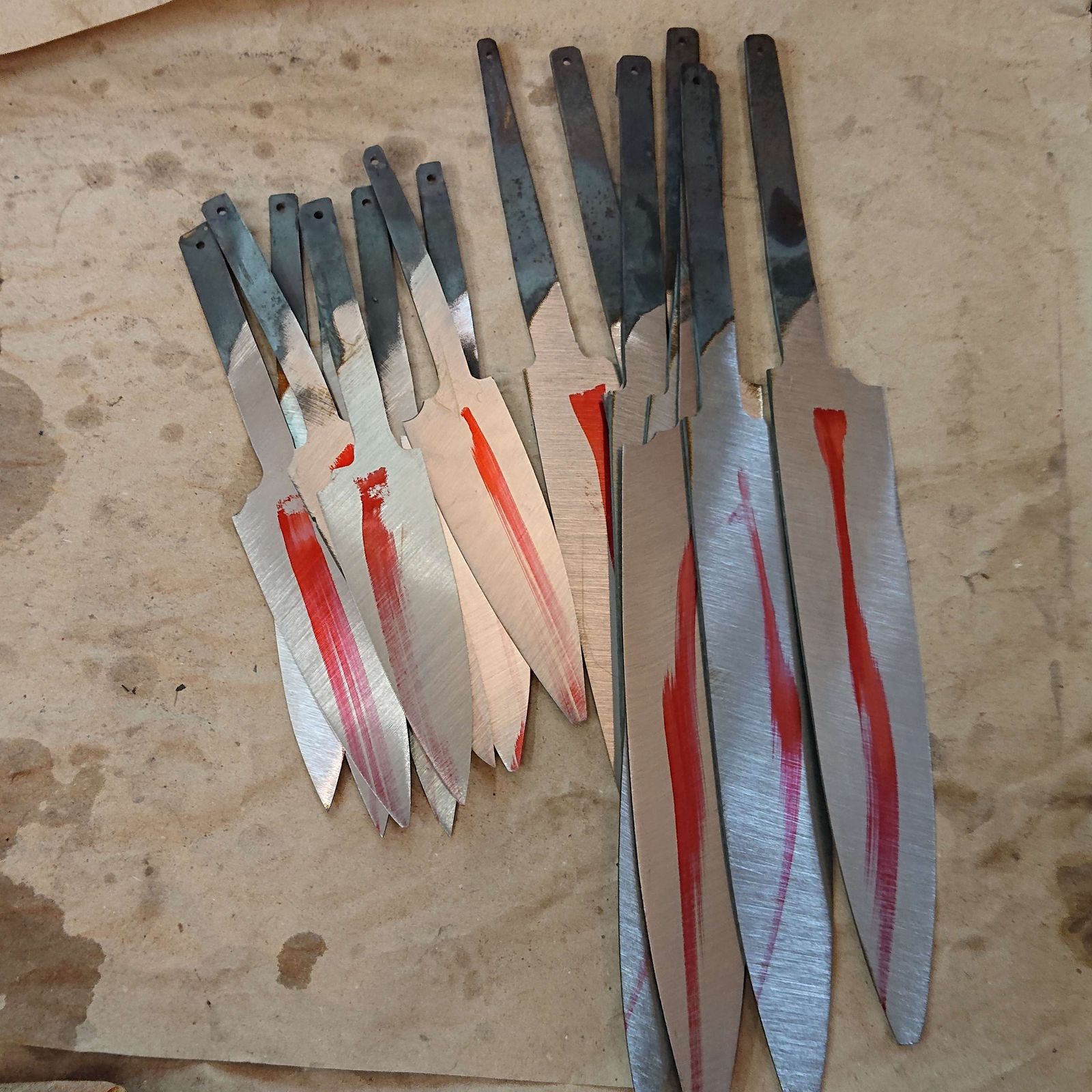
Polishing thus begins de facto by flattening the blades again on a P60 ceramics belt (point up). Then I mark all sides to keep track of things and I grind all blades on a P80 belt (point down) until all P60 scratches are removed. After that, I thoroughly check that they are really removed, and if not, I mark the problematic spots, grind them, etc. When all P60 scratches are truly removed, I go up to the P100 ceramics belt and repeat the process. Then P120 ceramics belt, then zircorund belts (P120, P150, P180, P240, P320) and finally one trizact belt (A65). With the trizact belt, I grind at a right angle to the blade spine until it has uniformly only this belt's scratches along the whole length.
And these few sentences describe a long period of incredibly tedious, boring, and difficult work. Even with active dust collection, I have to wear a face mask, face shield, and a scarf/cap to cover hair, and noise protection. And even though with N690 it is nearly impossible to ruin the temper by grinding, it is good to maintain proper working habits and I need to cool the blades (and sometimes the belts) with water. Thus I have wet hands all the time. I can't wear leather gloves - I am in no hurry to find out what would happen if a tip of a glove got caught between the belt and a wheel – and nitrile gloves won't last even five minutes, so my fingertips shrink from water. And constantly checking the ever more shiny surfaces for scratches hurts the eyes.
Simply put it is monotonous, mentally and physically taxing work and I cannot do it for long since loss of attention could lead to serious injury. When I start to think "I will finish this and then take a break" it means I should be taking the break already. It took me a whole week to get through all those abrasive belts before the blades were ready for the next phase.
And btw, polishing is also the most expensive step with regard to the material – I have destroyed approx. 12 belts, ca. 4,-€ each.
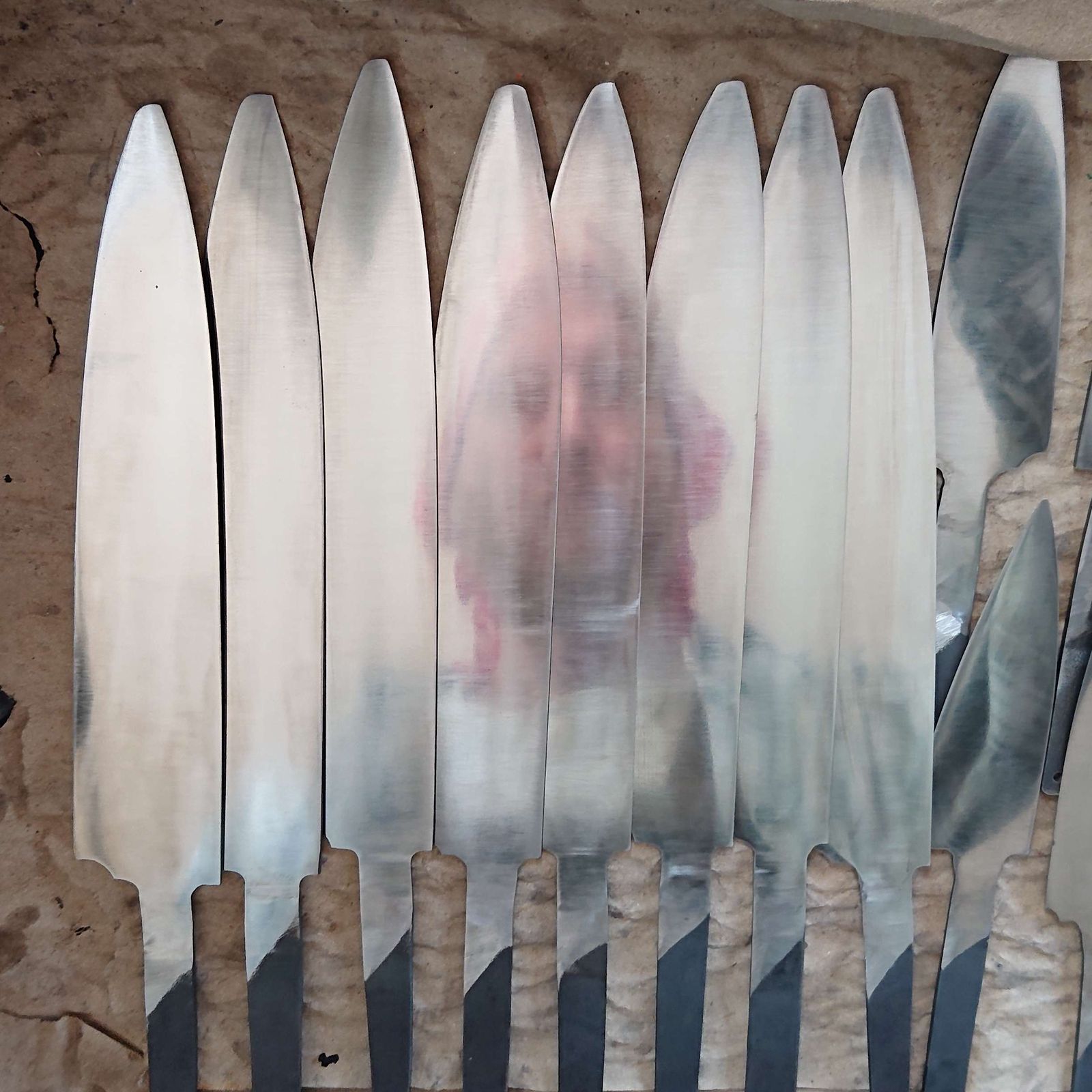
Ttizact A 65 leaves a relatively uniform and shiny surface with some degree of mirroring and this surface finish is often used for both machine and handmade knives. I do not like it though, it looks too artificial. So I am using two main types of finish for my knives – mirror polishing and tumbling. Mirror polishing I am using for high-end luxury knives and it consists in going up the trizact belts and then to very fine abrasive grits, essentially doubling the amount of manual work. For kitchen knives, I use mostly tumbling.
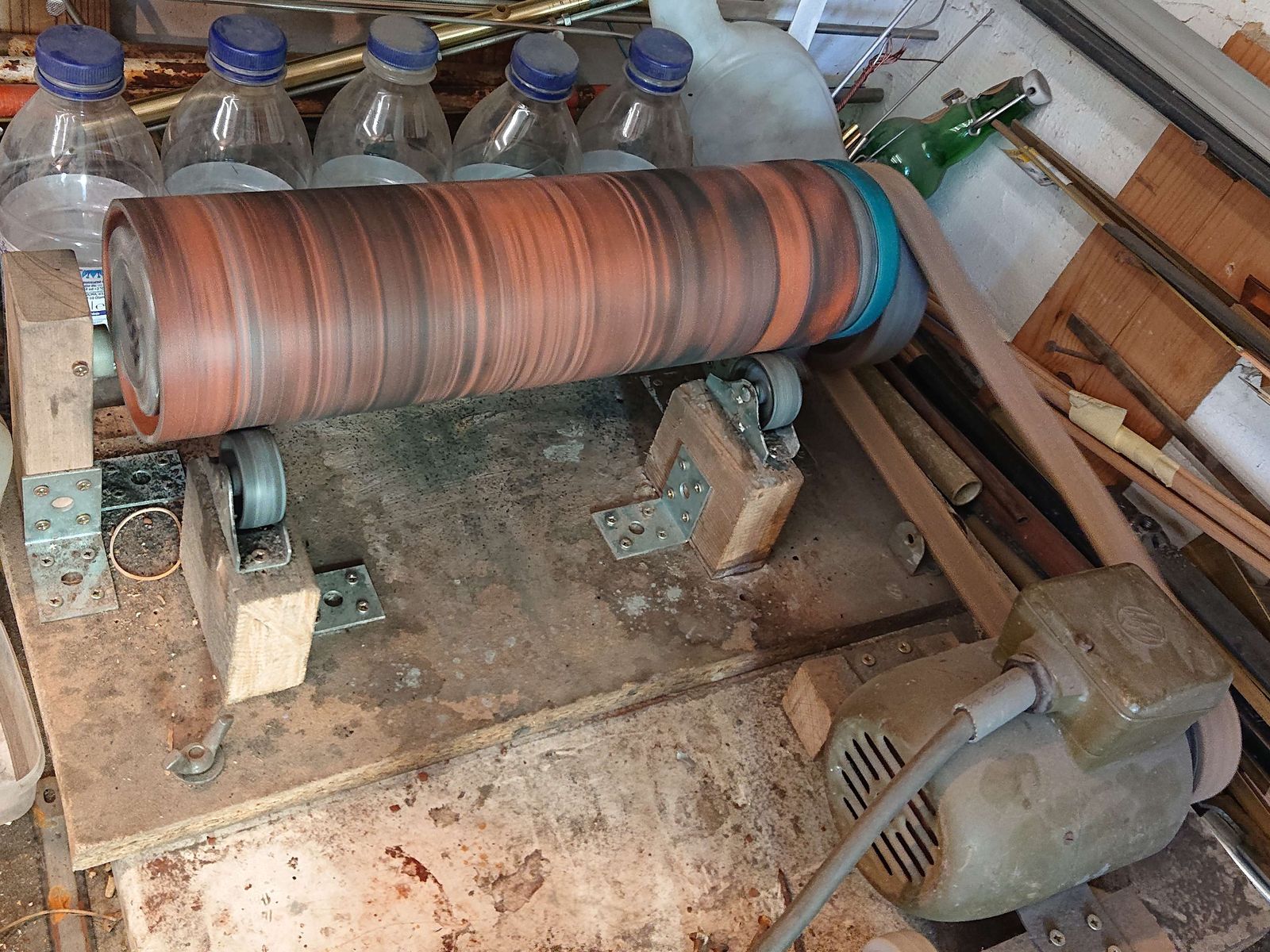
For tumbling I put the blades into a drum with fine sand and rotate them as long as it takes to get a mostly uniform surface – usually a week to week-and-half. This creates a very natural-looking surface without obvious scratch patterns. After this, I put the blades into another drum with hematite powder and crushed coconut shells. This creates a very fine, satin surface.
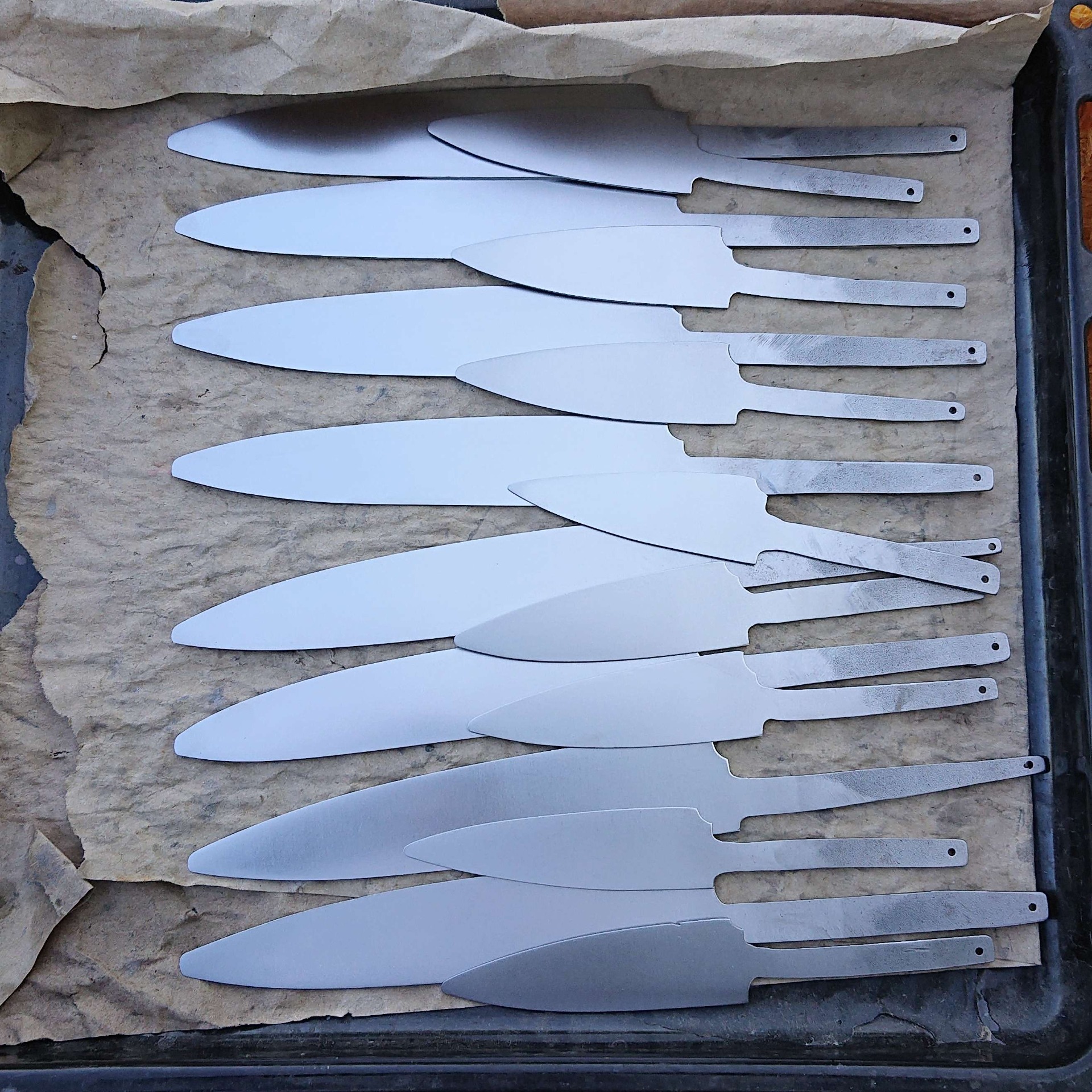
Tumbling is my favorite production phase since a motor does all the work and I can do something else – like choosing wood for handles and blocks.
And about the wood that I intend to use for these knives, I will write next week.