Making a Commission - Part 2 - Outlining
Having templates allows me to start the actual work, so let's go.
Well, the actual beginning of the work is the straightening of steel profiles which usually come slightly bent because they are stamped/sheared. I will describe the actual straightening process at another time because this time the steel was already straight – I got used to straightening the steel on delivery in order to be able to start work without delays whenever I decide to make something. So the beginning was this time scratching out approximate blade outlines on one of the two used steel profiles. Then I drilled in both pieces four holes, outside of the future blades and as close to the edges as possible. These four holes allowed me to screw the steel profiles together so I could drill the 5 mm holes at tang transitions and 14 mm holes at the blade heels in both pieces at once, saving time.
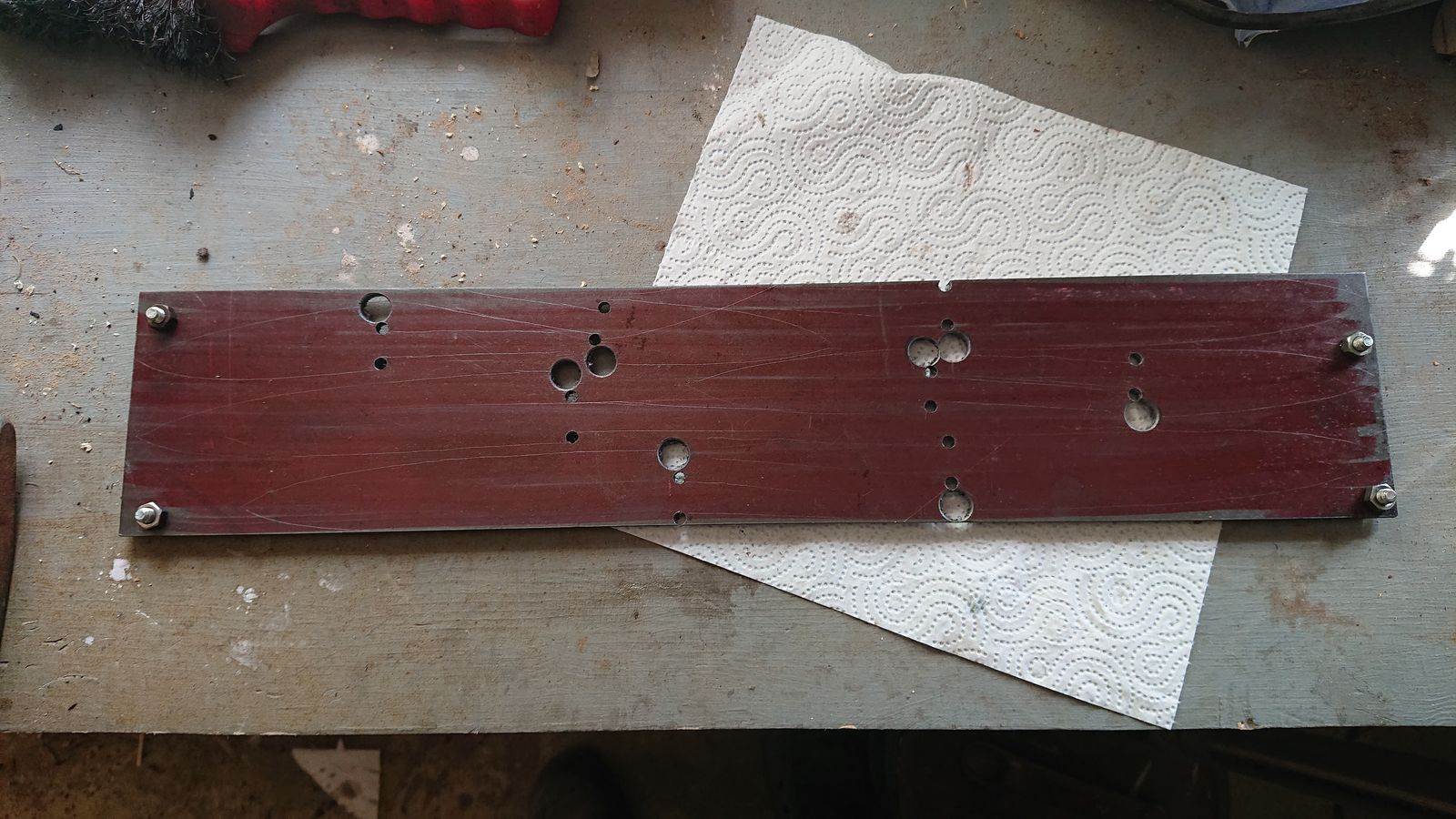
Unfortunately, I forgot to take a picture of the following step – cutting out very rough profiles with an angle grinder. In essence, I started at one of the shorter edges and progressed carefully to the other, cutting 1-2 mm outside the outlines, until I had all 16 very rough and angled pieces. After that, I spanned a blunted 60-grit belt into my belt grinder and I de-burred all edges. Strictly speaking, de-burring the edges is not necessary but I cannot use gloves when working with the belt sander, and working bare-handed with pieces of steel full of burs from an angle grinder is neither comfortable nor safe.
Using the templates I have re-drawn precise-ish outlines on all of these rough pieces and I ground them out to nearly the final outline on the belt sander, again using old, worn belts.
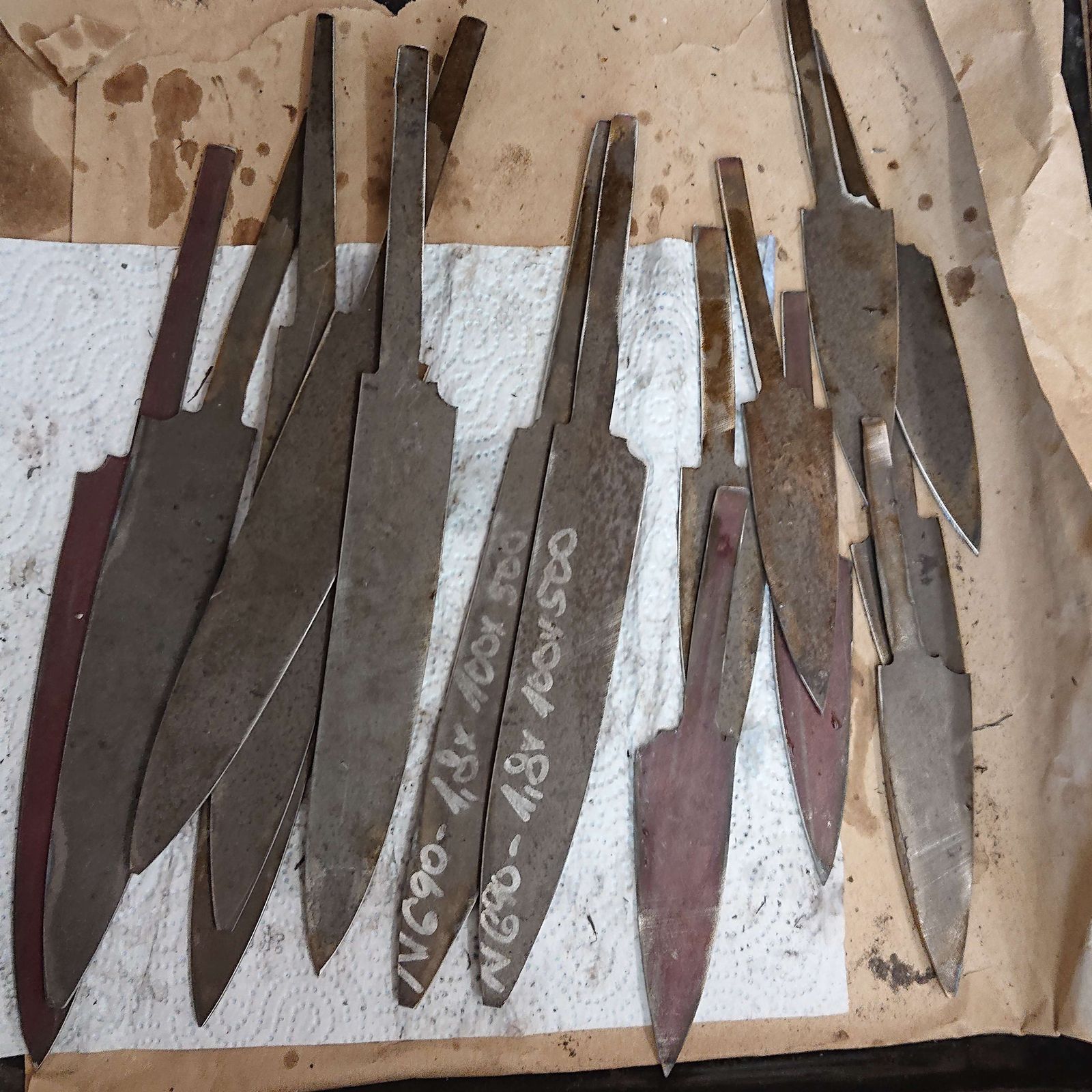
I am using worn belts for de-burring and outlining because this destroys the belts very quickly. And whilst blunt belts overheat the steel, that is not an issue at this stage and this is a way to get squeeze some use out of an old belt before having to discard it completely. A worn belt also removes the material more slowly so there is less of a risk to remove more material than desired.
The outlines are now only approximate and mostly slightly larger than the final blade. All tangs are bent slightly upwards like they are drawn on the templates (and they are not cut out very precisely either). This allows for getting more blades on a flat steel bar, but the tang position is now inconsistent between the pieces and nowhere near where desired. Thus it is necessary now to slightly bend the tangs downward. After the tangs were tuned, I drilled 3 mm holes into their ends, ending up with sixteen flat blade outlines in steel.
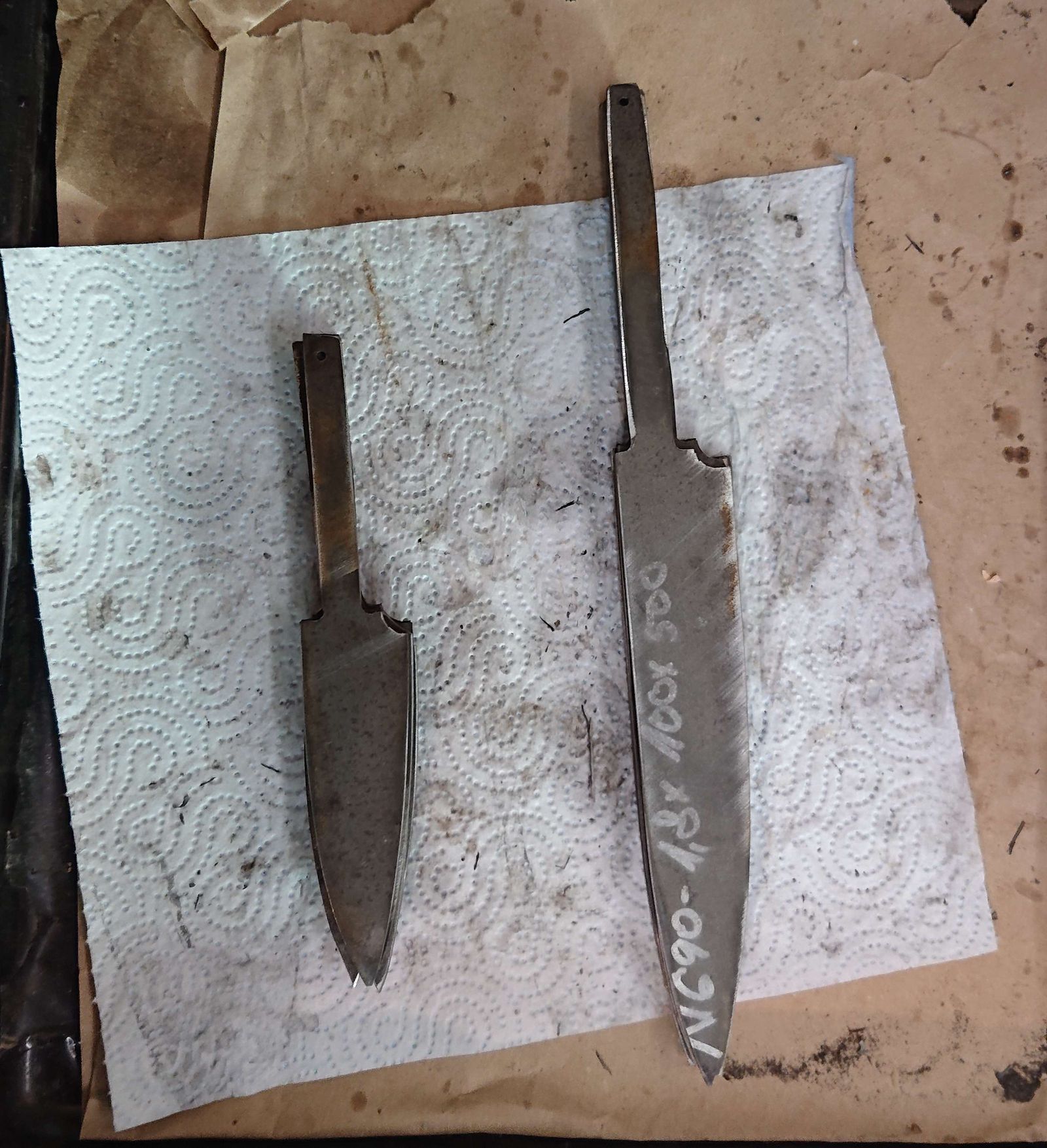
The tangs are now mostly in parallel with the back of
the blades and all profiles are the same within a few mm. Although not
identical because my goal is to make 8 unique sets, not 8 identical
ones.
Next week we shall progress with profiling the blades.