Making a Commission - Part 1 - Design
I am working on a small commission and decided it won't go amiss to document the process.
It began with a previous
commission – a set of two kitchen knives of which the smaller one
was made from an offcut without a prior plan. The actual commission is
for a pair as similar to this one as possible, including the block
with a foldable leg.
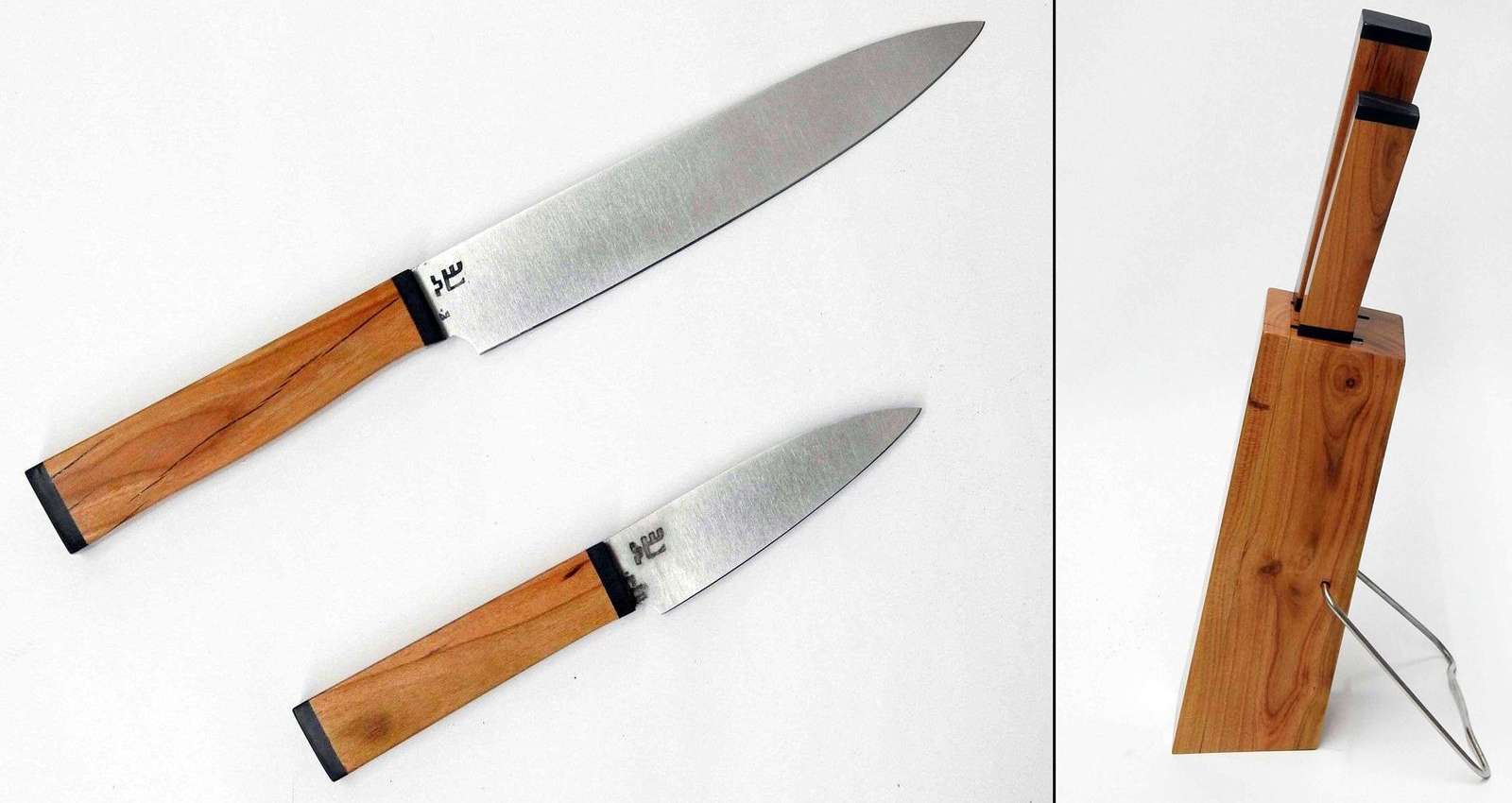
I did not expect to make this set again so I have no templates and measurements, so I have to begin almost from the start. And the start is a design and a template. In this case, we are talking about two universal kitchen knives with a point. Minimalist simple blade design without ricasso, ridges, or fullers, and with a flat grind. Rat-tail tang.
I draw templates on an mm
grid in Photoshop, although I made do with a pencil and grid paper in the past. For one-off projects, I do not bother reinforcing the
template after printing but for projects that I intend to make again, I laminate it so it can resist the harsh workshop environment better.
The circles define the position of holes drilled into the flat
profile before cutting the outlines (5 and 14 mm) or into the tangs
of prefabricates (2,5 mm).
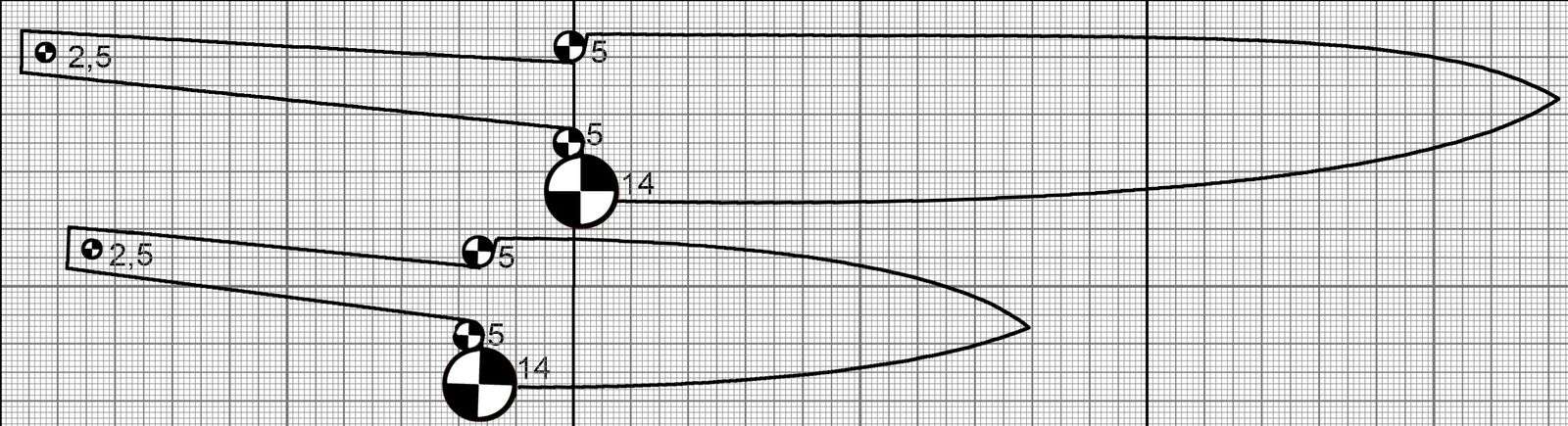
Pre-drilled holes have multiple functions. The 5 mm holes define the radius at the transition from tang to blade. Radius here helps to distribute and relieve material stresses – a sharp angle would significantly reduce the strength of the blade at this point and it could easily crack, it could even crack during the manufacturing process during quenching. 14 mm holes define the radius at the heel of the blade. It is easier to establish a nice curve by drilling now than by grinding later. And all these holes together help cut out the blade outline from flat steel.
And since just two
knives would be barely worth heating the forge, I have decided to
make as many knives as I can from two 1,8x100x500 mm flat profiles.
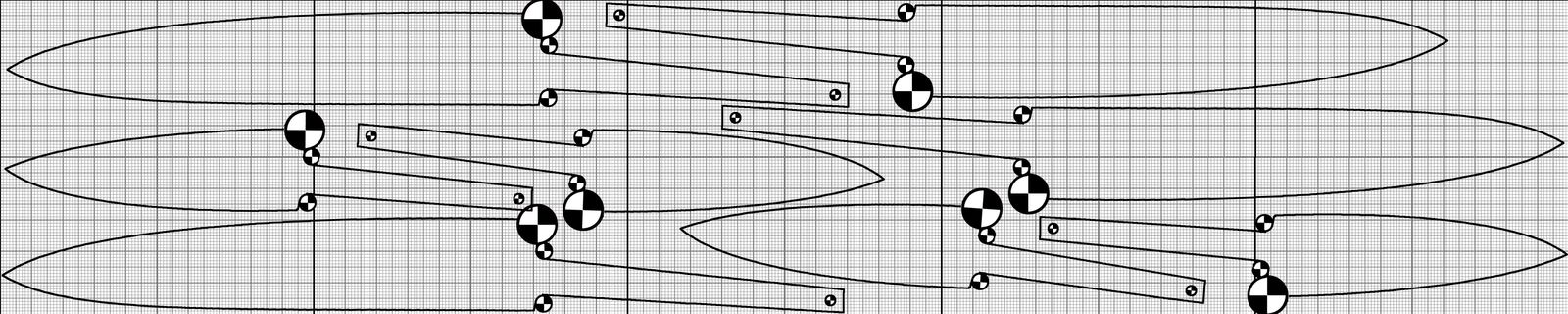
I have managed to squeeze in there 4 big and 4 small knives on one profile, and it was not completely easy – I got in 4 small and 3 big ones in there easy enough, but the fourth big one, to round it off into whole sets, was giving me some trouble. In theory, I could make the tangs shorter but shorter tangs make some manufacturing steps awkward or even dangerous, so I am leaving myself at least 7 cm (nearly palm-width) of material to hold on to. Positions of the tangs on the flat profile are just approximate at this stage– it is possible, even necessary, to bend and re-shape the tangs into desired positions and shapes before hardening anyway.
From two profiles it
should thus be possible to make 8 sets. The ordered set will be made
from cherry wood and buffalo horn just like the original. I will use other species for the
remaining 7 sets (or fewer in case something goes wrong). I am already looking up pretty pieces of wood so each
set is unique.
To be continued in a week.