Cutting Boards - Part 5
After finishing my first kitchen cutting boards I decided to make a "maxiboard". Not for cooking but for leather work. Hopefully it will hold longer and better than any cutting mat from office supplies. I decided to use black locust wood because it is cheaper and more readily accessible than Jatoba. And it is hard enough for any work.
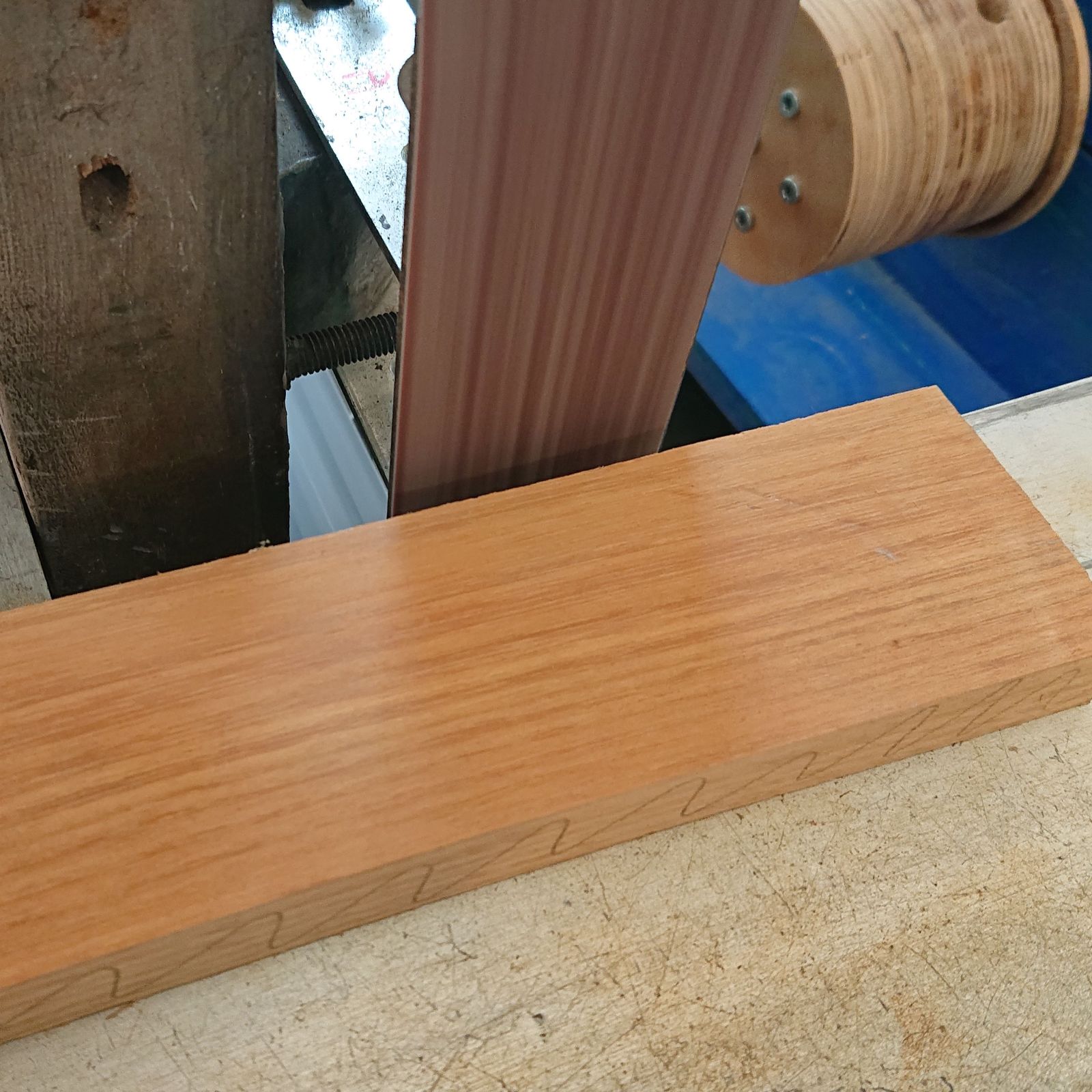
The used offcuts were nearly the same size as those from Jatoba that I used for kitchen boards. I did not need to cut them to size but unfortunately, they did not have right angles all around and the sides were not completely flat. The first step was thus to grind sides at right angles.
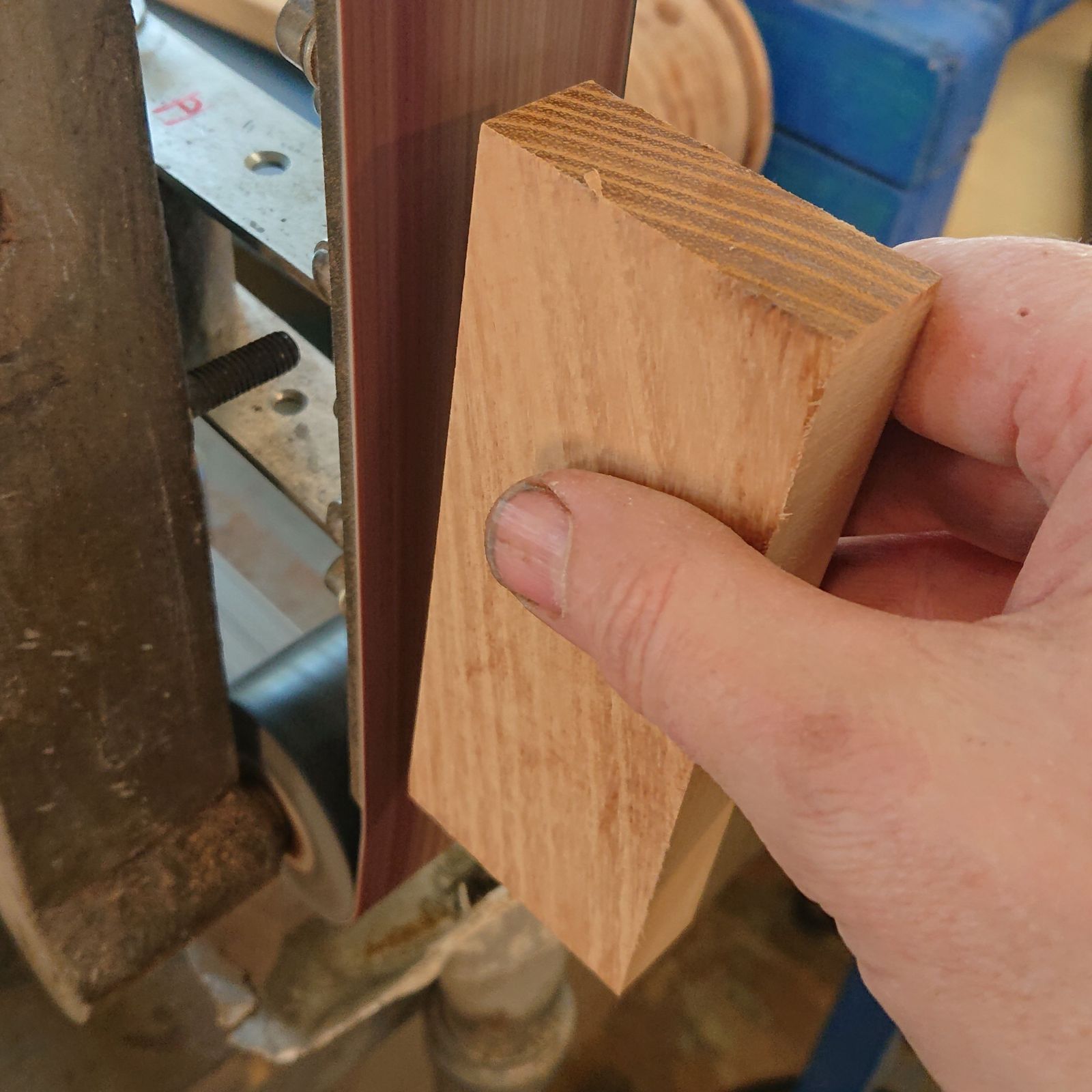
And the second step was to flatten the now right-angled sides. Mostly it was enough just to touch them up with a belt sander but for a few pieces I had to use elbow grease and flat stone.
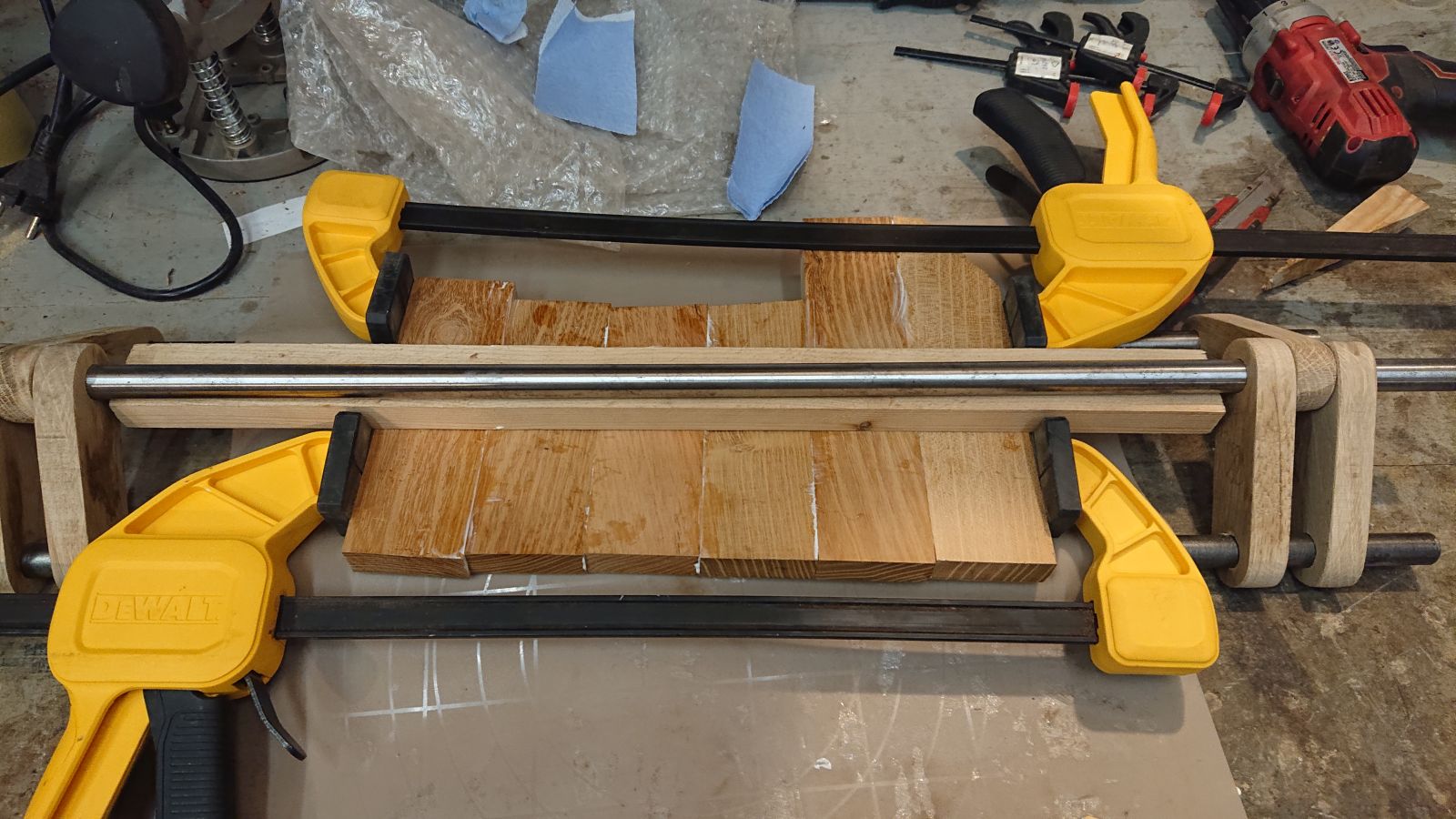
Gluing the offcuts together is not exactly easy. They do have a tendency to creep, especially at the beginning before the glue excess gets squeezed out and the glue sets a bit. To make the work easier I made a jig from three pieces of pipe and six pieces of wood. I can put a row of the offcuts on the two lower pipes and press down on them with the upper pipe (for thinner boards with a wood offcut in between as shown in the picture). It holds the pieces reasonably flat.
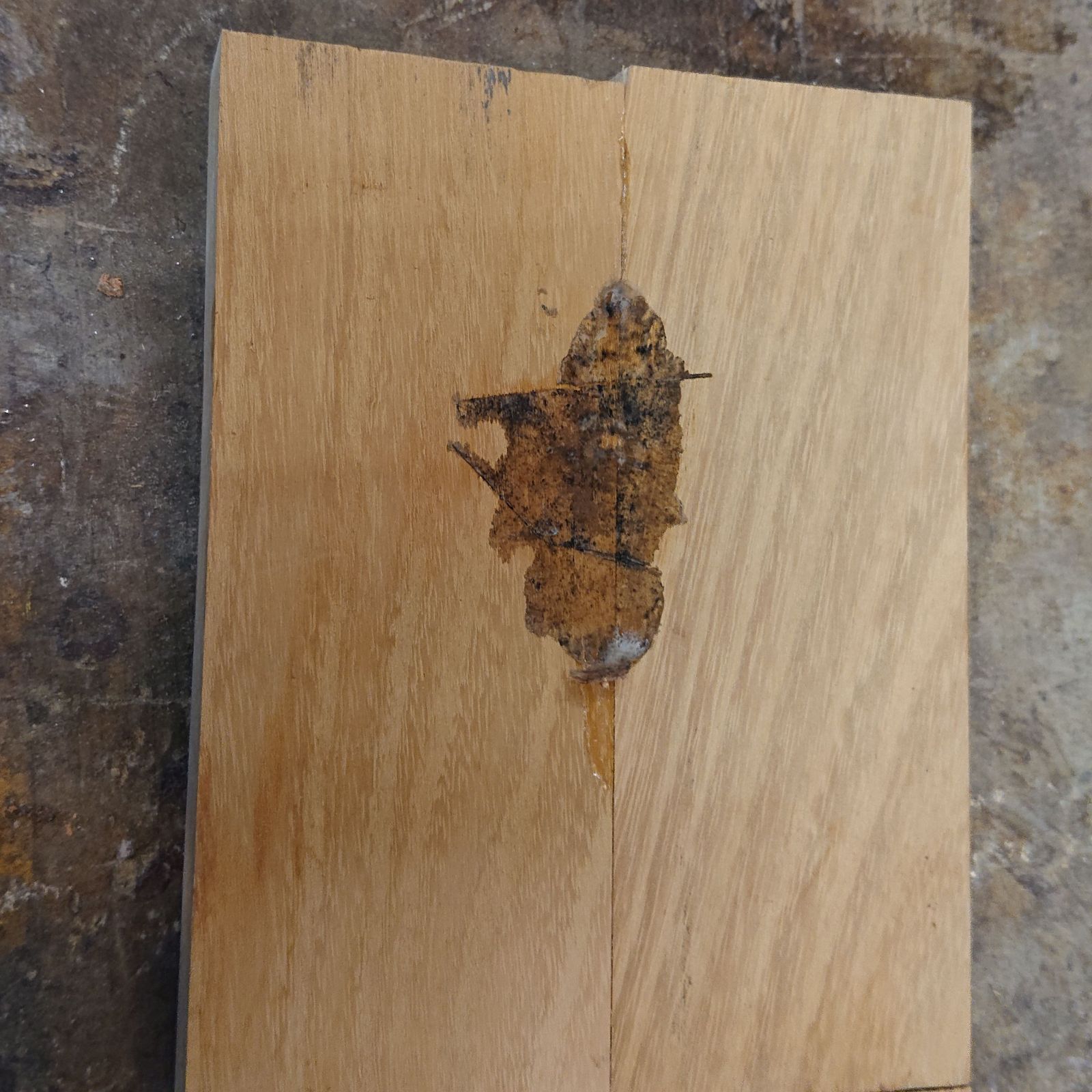
Unfortunately, I forgot that black locust wood must not come in direct contact with iron when being glued. Because water-based glue + iron = iron ions, and iron ions react with tannins from the wood and dye the glue (and in sufficient amounts the wood) to black. In this specific case, it is not a problem but I must be careful in the future. Black locust wood is not the only wood that does this, jatoba and oak do it too.
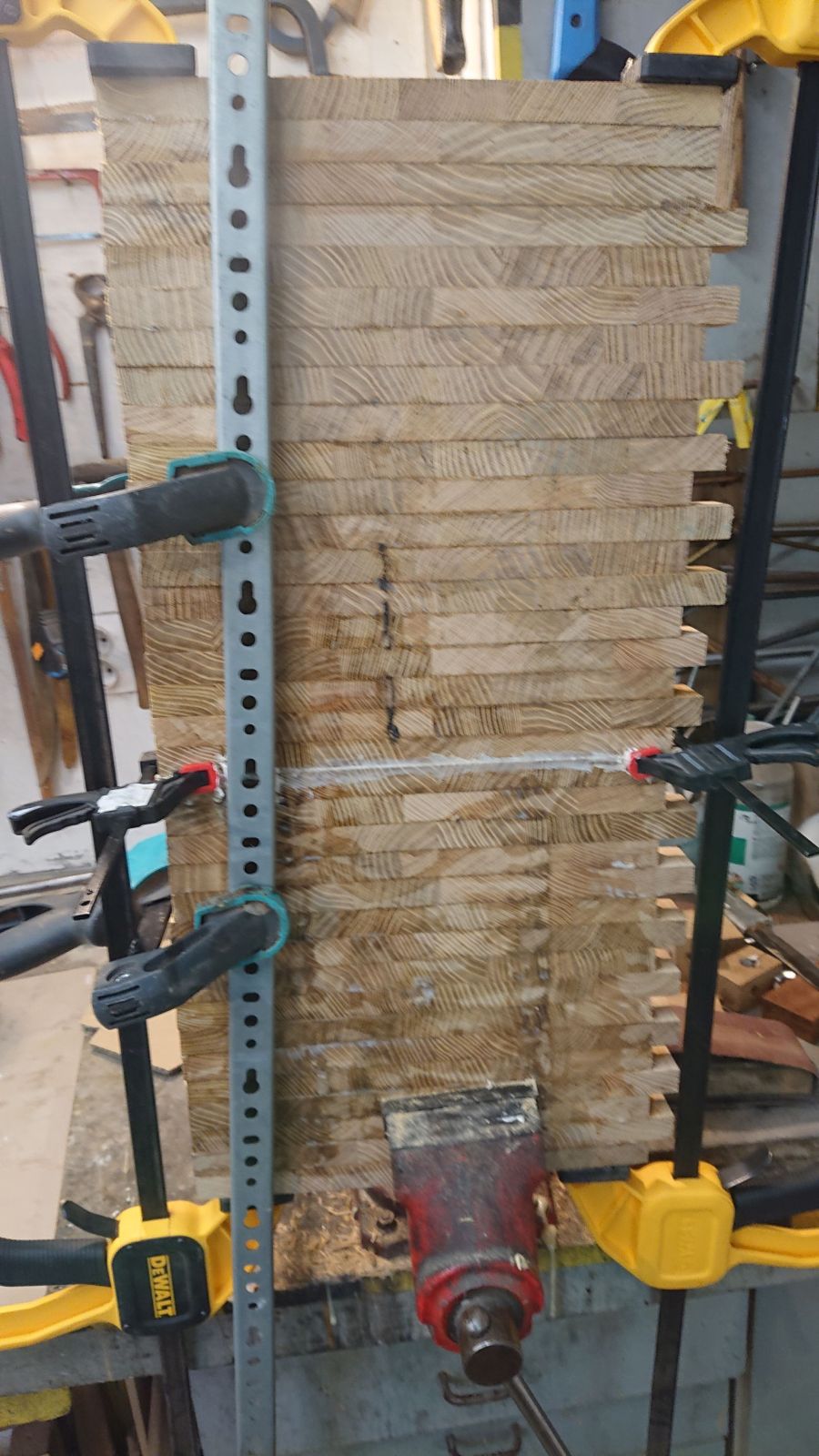
After gluing the offcuts into small boards I cut those into stripes across the grain and sanded them all to the same thickness. And with the help of the jig from old pipes, I glued those stripes together. However, the goal was to make a 60 cm wide board and I could not fit all that into the jig, so I had to glue it in halves and then connect those together in the vice. I am not expecting to make another board this big, it would not be very practical in the kitchen.
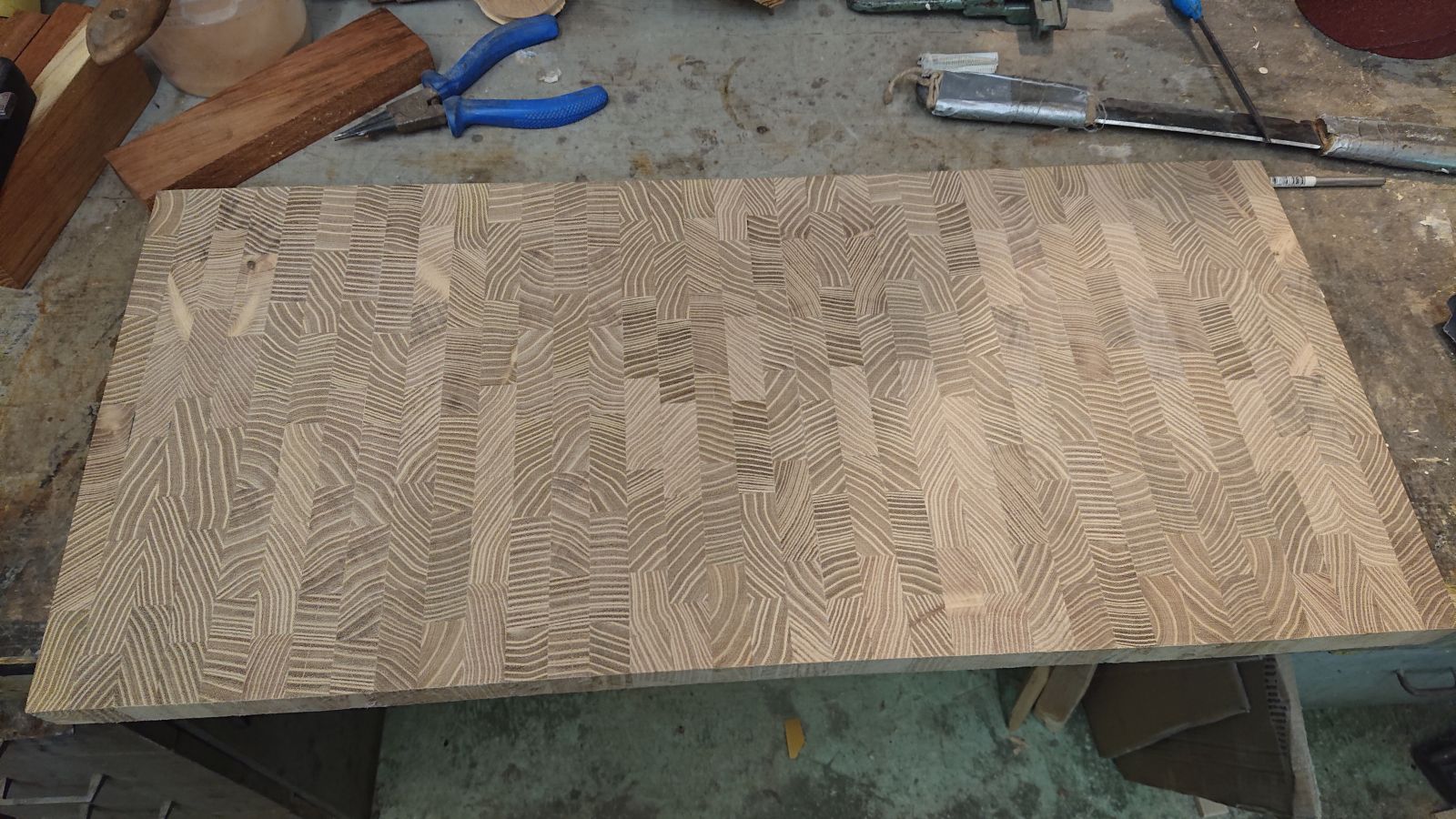
And it was when flattening and sanding this board when my drum sande broke. After the repairs, I could continue and I sanded the surfaces all the way to 120 grit. I must say, I like the way the growth rings look on this one.
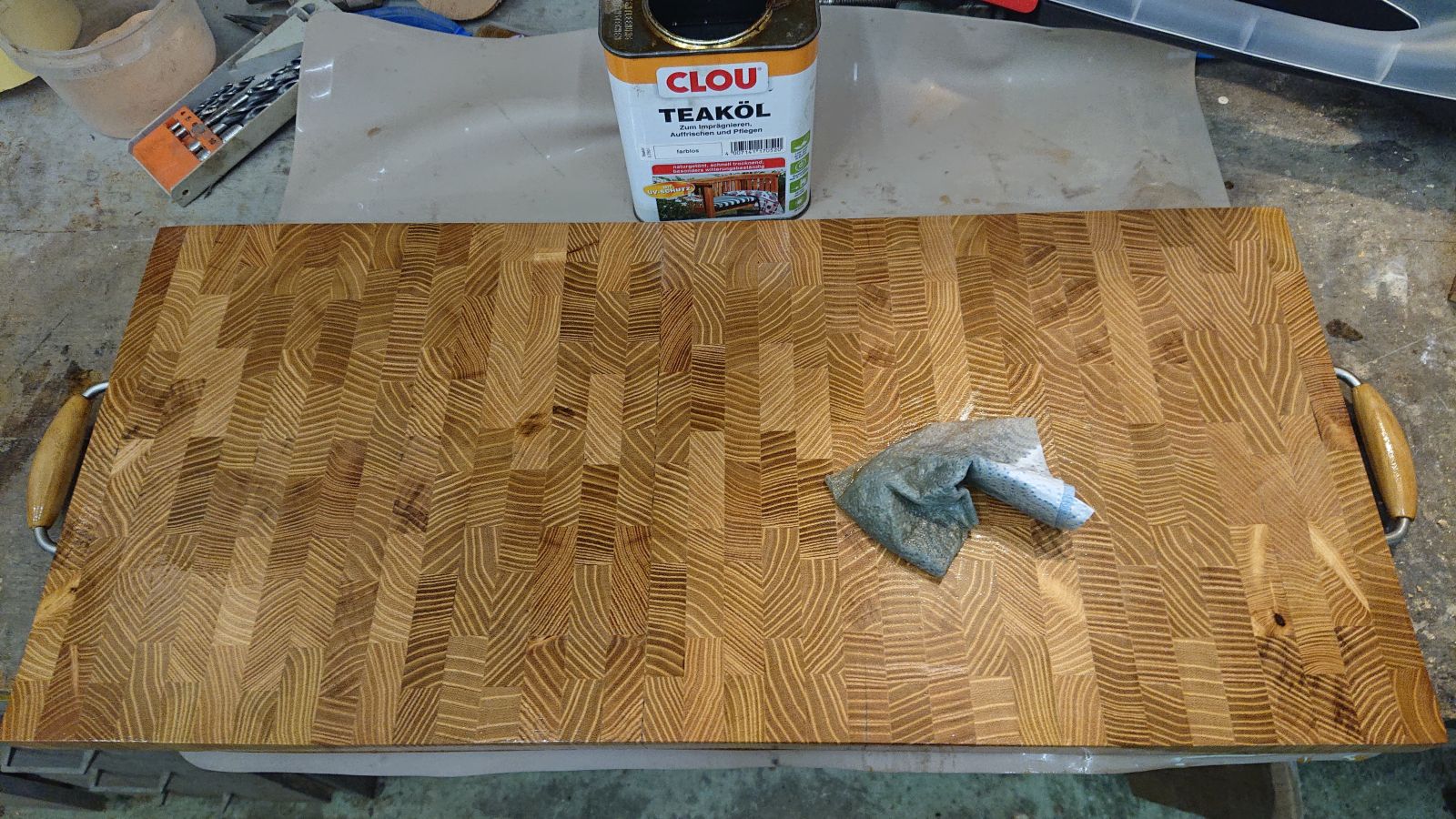
I
added two handles because I do expect to have to move it with stuff
on it. One side will be used for work, and the other I intend to use as a
background for knife photography. And because this board will not be
used for cooking, I used ordinary drying oil for the surface and not
the special food-safe one. After the first oil layer dries, I will
apply a second one and it will be done. In the meantime, I already
started work on another batch of boards from Jatoba.