Making a Commision - Part 9 - Gluing the Bocks
With the project being more than half-finished, metalworking shifts to woodworking – making the blocks and handles. And this started by squaring off the wood on the table saw.
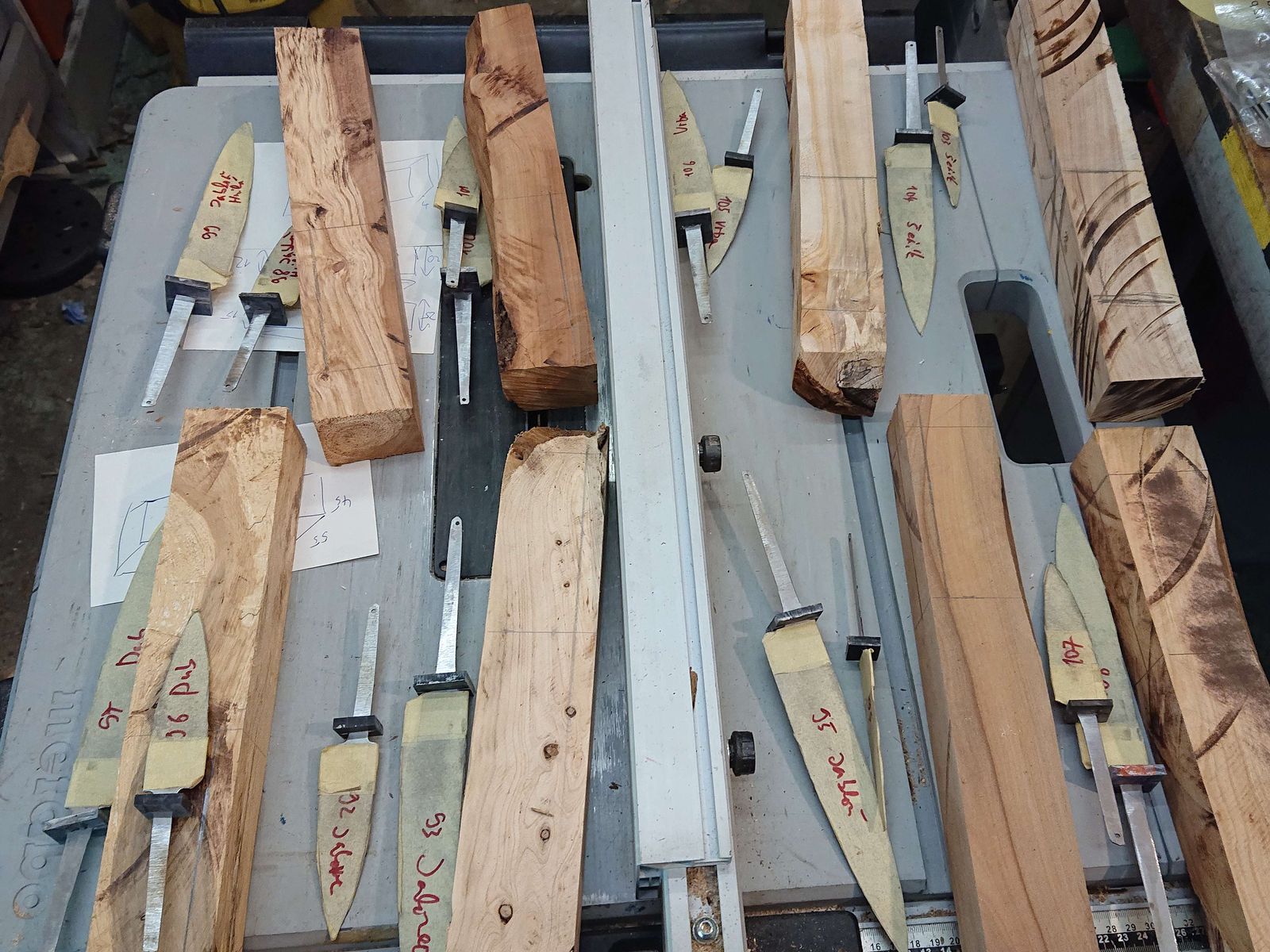
Whilst doing this I have unfortunately found out that the lilac piece I originally chose is not big enough – lilac tends to twist and warp during drying and after I squared the sides on this piece, there was not enough left to make both handles from one piece. Luckily I have found another piece in my stockpile, so no drastic changes were necessary and it only cost me a bit of time when searching and squaring a new piece.
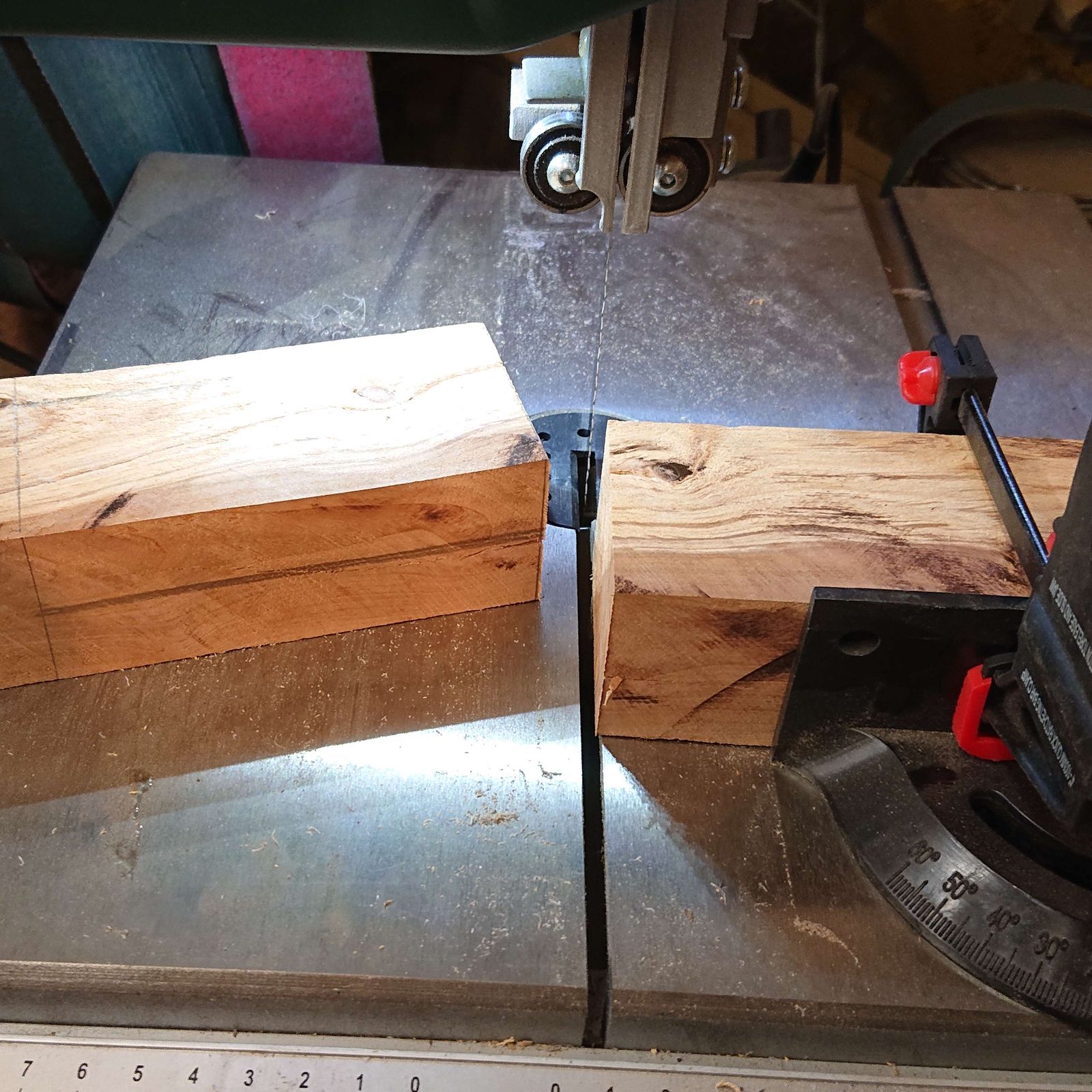
Once the wood was squared off, I could move to the band saw. I cut off two pieces – 19 cm for the block, and 11 cm for the handles. From the piece meant for the block, I further cut off about 1 cm thick stripe from the future top side of the block. From the piece for handles, I cut off the same thickness and then I parted the remaining piece into two halves. That way – with a bit of care – the wood grain in the handles will be a continuation of the wood grain in the block, making it evident that it is all made from one piece.
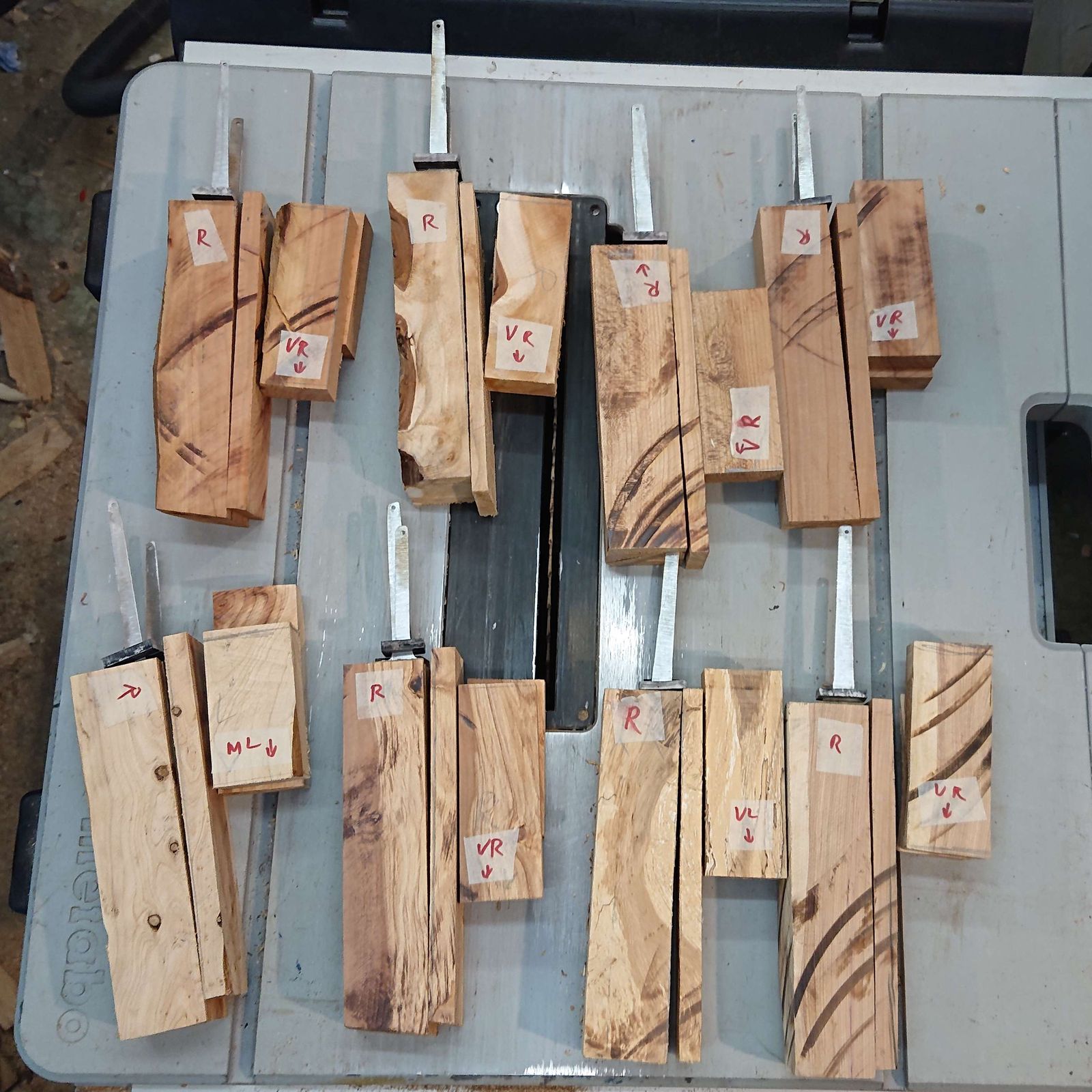
Back on the table saw again I cut 2 grooves into the bigger piece meant for the block, to the depth corresponding to the blades' width. And since cutting on a band saw is never completely straight and clean, I had to flatten the two planes that were meant to be glued by sanding them on coarse abrasive paper glued to a granite tile.
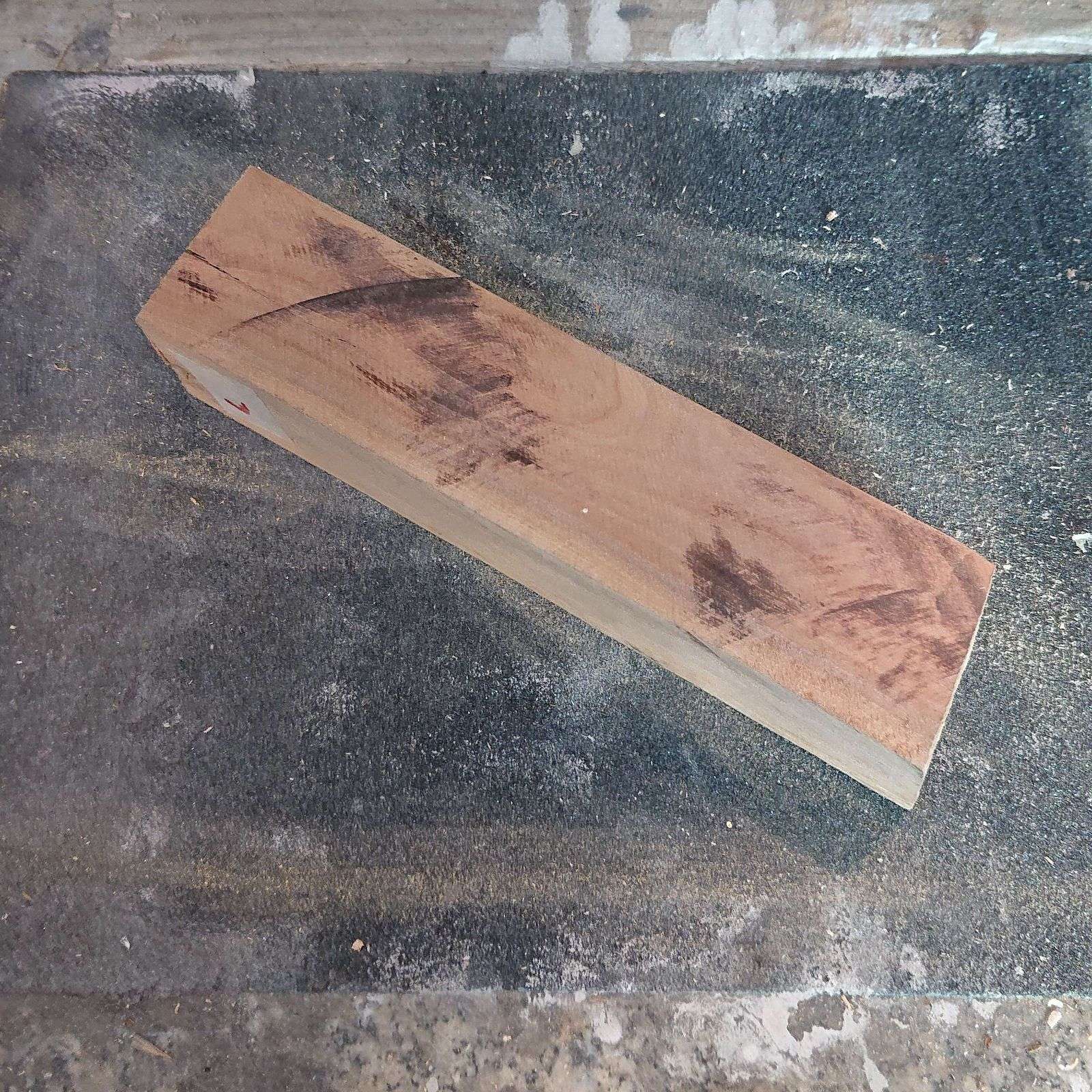
Flat planes can be glued directly, but to improve the strength of the joint it is good to coarsen them a bit, so I scraped ridges in both of them with a hacksaw blade. That increases the surface by almost half and thus ensures a stronger joint.
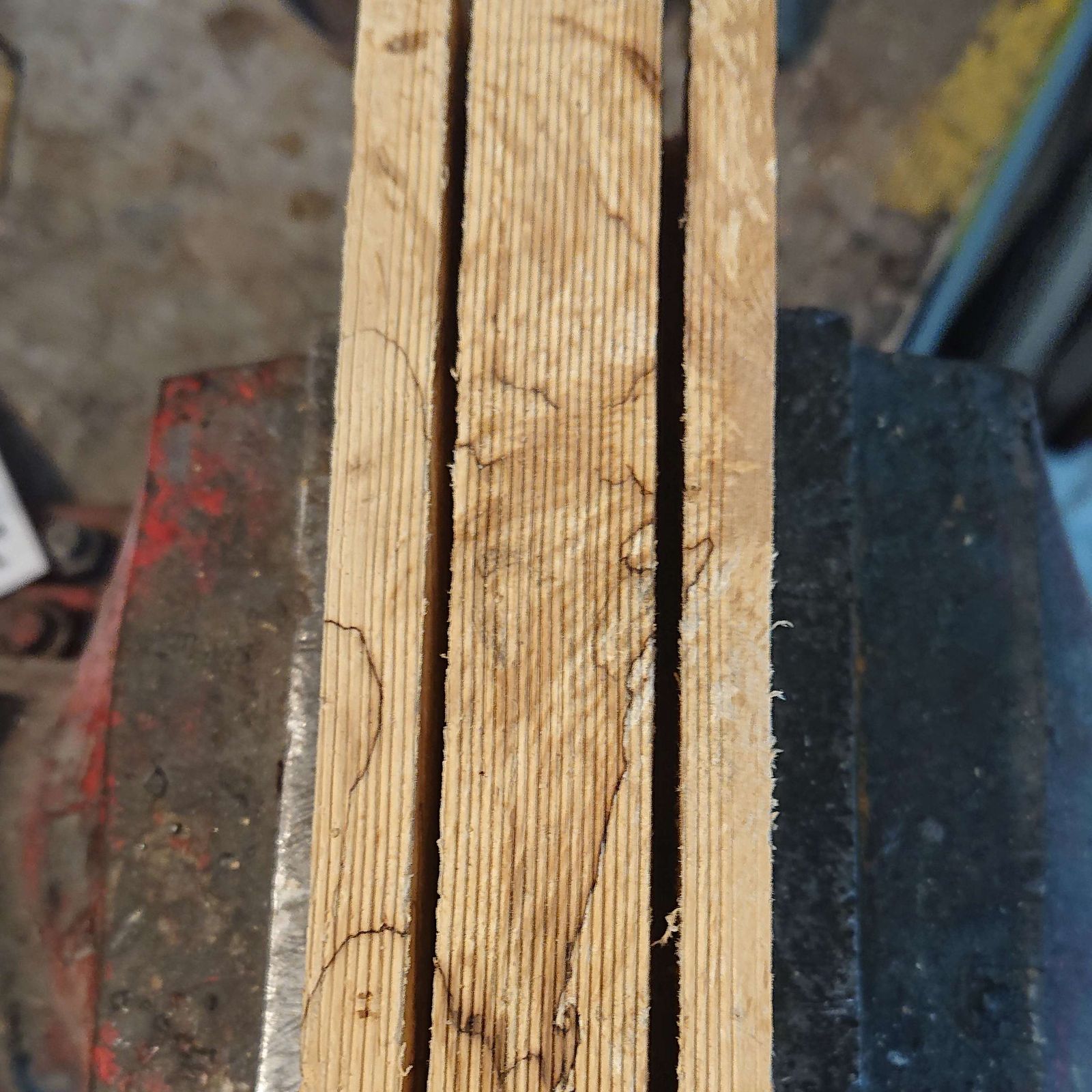
I have used waterproof PVA glue for the joint. Waterproof glue is not, strictly speaking, necessary, but since the end-product is meant to be in a kitchen where it can encounter steam or water, it is better. In colder weather, I would use polyurethane glue and if I were gluing stabilized wood, I would have to use epoxy. PVA is the best option, it does not tend to clog up the grooves for blades (something that the PU glue does a lot) and it is cheap.
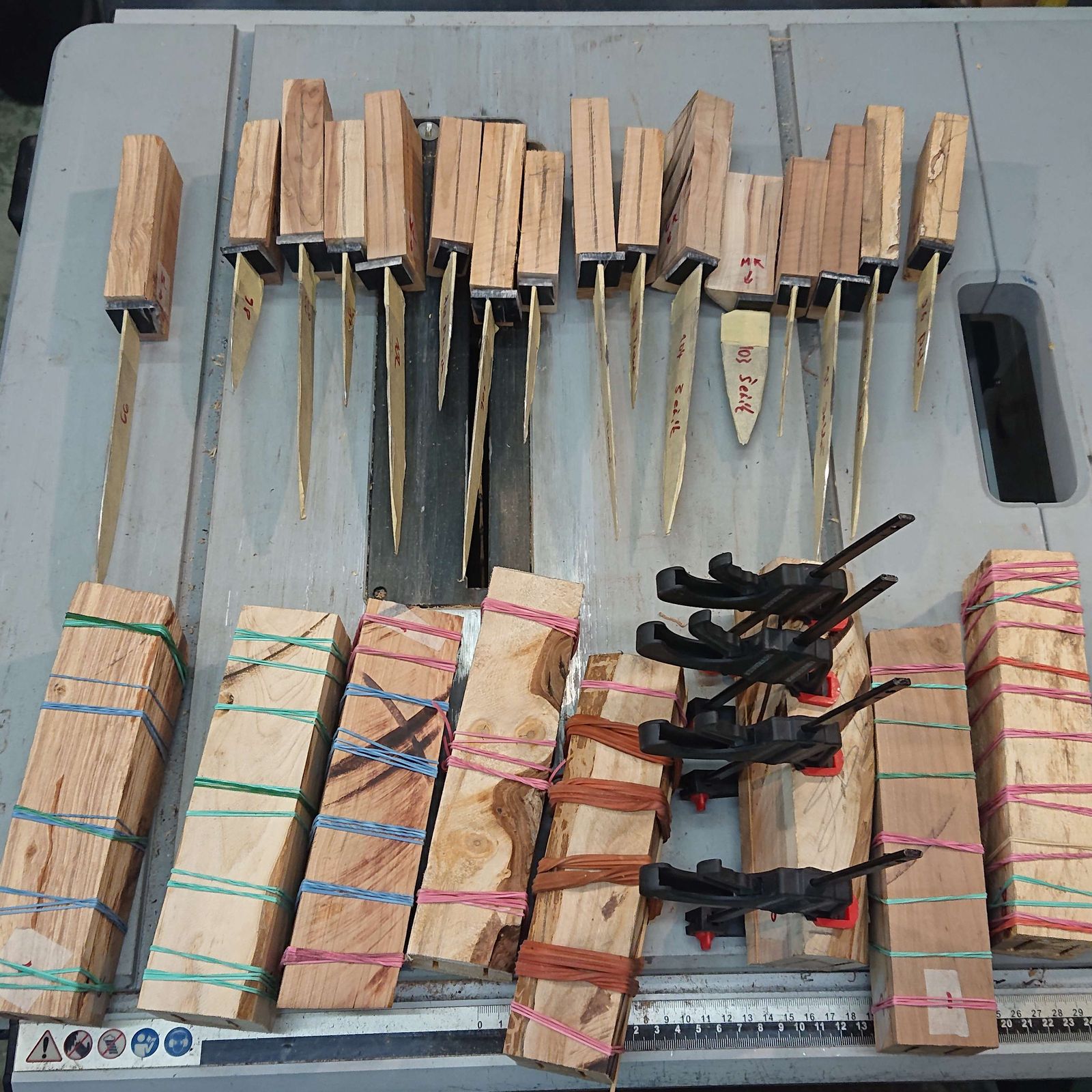
The rubber bands exert sufficient and relatively uniform pressure. Only the lilac piece was held together with clamps. Cutting and sanding mean that the grains on glued parts can never perfectly match again. For most of these, it is not a problem since the grain is not too visible, but the lilac piece had lilac-colored streaks in the heartwood and I wanted to match at least those on the front face, so I used the clamps. The goal is for the glued joint to be as little visible as possible and the clamps allowed for more precise positioning of the parts relative to each other.
In the last picture, you can also see some pre-assembled knives. About that next week.